What Does A Vertical Roller Mill Do
Vertical Roller Mill
A vertical roller mill is a type of industrial equipment used for grinding raw materials or finished products into fine particles. It consists of a large cylindrical drum mounted on a vertical axis, with grinding rollers positioned inside. The material to be ground is fed into the mill, where it falls onto a rotating grinding table. The grinding rollers, which are pressed against the table by hydraulic or pneumatic systems, crush the material into a fine powder. The ground material is then separated by a dynamic classifier, allowing only the desired particle size to pass through while larger particles are returned to the grinding table for further processing.
Applications of Vertical Roller Mills
- Cement Industry: VRMs are widely used in the cement industry for raw meal grinding, coal grinding, and cement grinding. They help achieve the desired fineness levels, enabling the production of various types of cement, such as Portland, blended, and specialty cements.
- Power Industry: In power plants, VRMs are employed for grinding coal into fine particles to enhance combustion efficiency. The ground coal is then used as fuel in boilers to generate steam, driving turbines and producing electricity.
- Mining and Minerals Processing: VRMs play a crucial role in the mining industry by processing ores and minerals, such as limestone, gypsum, and bauxite, to produce desired particle sizes for various applications like cement production, filler materials, or chemical processes.
- Other Industries: VRMs are also used in other industries, such as metallurgy, chemical, and ceramics, for grinding and processing raw materials, enabling the production of various end products.
Benefits of Using Vertical Roller Mills
- Energy Efficiency: VRMs have a reputation for being energy efficient, as they use a lower amount of power compared to other grinding systems, such as ball mills. The grinding pressure exerted by the rollers on the material reduces the need for internal circulation, leading to lower energy consumption.
- High Grinding Capacity: Due to their large grinding surfaces and high grinding pressure, VRMs can handle higher capacities, allowing for increased production rates and reduced downtime.
- Consistent Product Quality: The dynamic classifier and adjustable grinding pressure in VRMs ensure that the final product has consistent particle size distribution, meeting industry standards and customer specifications.
- Operational Flexibility: VRMs can handle variations in feed size, moisture content, and hardness, allowing for seamless operations even with changing raw material characteristics.
- Reduced Maintenance: The modular design and wear-resistant materials used in VRMs result in extended service life and reduced maintenance requirements. Furthermore, the hydraulic or pneumatic systems used for applying grinding pressure simplify the process and reduce the need for mechanical adjustments.
- Environmental Benefits: VRMs contribute to reducing CO2 emissions and energy consumption by enabling more efficient grinding processes. The improved particle size distribution reduces the need for additional grinding stages, decreasing the overall environmental impact.
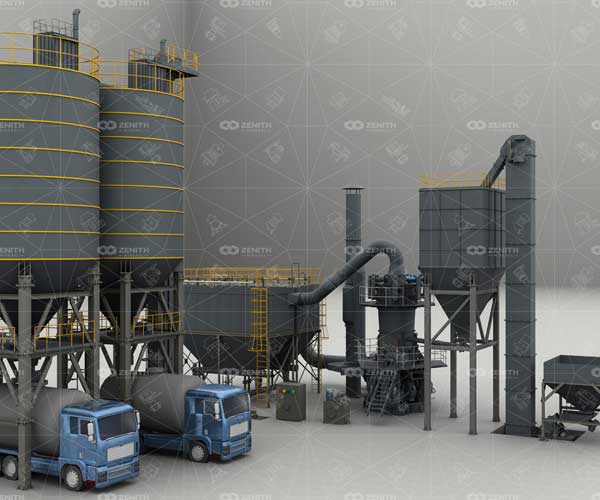
What Is The Feed Size Of A Vertical Roller Mill
The feed size of materials entering a vertical roller mill (VRM) plays a critical role in determining the efficiency, output, and overall performance of the grinding process.
Feed Size in Vertical Roller Mills
Feed size refers to the dimensions of the raw material particles entering the VRM for grinding. It is a crucial parameter that affects the VRM’s grinding efficiency, energy consumption, and product quality. The feed size depends on factors such as the type of material being processed, the desired product fineness, and the specific VRM design.
Impact of Feed Size on VRM Performance
- Grinding Efficiency: The feed size directly affects the VRM’s grinding efficiency, as larger particles require more energy to be broken down. If the feed size is too large, it may lead to reduced throughput, increased power consumption, and a decrease in overall grinding efficiency.
- Product Quality: The uniformity of the feed size influences the product’s final particle size distribution. A more consistent feed size allows for better control over the final product quality and helps ensure the desired fineness levels are achieved.
- Mill Wear: The feed size can also impact the wear and tear on the VRM’s grinding components. Larger particles can cause increased wear on grinding rollers and tables, leading to higher maintenance costs and reduced equipment life.
- Energy Consumption: As mentioned earlier, larger feed sizes require more energy for grinding. Therefore, optimizing the feed size can lead to reduced energy consumption, lower operating costs, and improved environmental performance.
Ideal Feed Size Range for Various Applications
The ideal feed size for a VRM depends on the specific application and the desired product fineness. Below are some general guidelines for various industries:
-
Cement Industry:
Raw Meal Grinding: The typical feed size range for raw meal grinding in the cement industry is 0 to 90 mm. VRMs can efficiently grind raw materials to a fineness of 10% to 15% residue on a 90 µm sieve.
- Coal Grinding: For coal grinding in cement plants, the feed size is usually between 0 and 50 mm, with VRMs capable of producing a product fineness of 12% to 15% residue on a 90 µm sieve.
- Cement Grinding: Cement grinding in VRMs requires a feed size of 0 to 30 mm, with the mills producing a final product fineness of 3000 to 5000 Blaine (cm²/g).
- Power Industry: In the power industry, VRMs are used to grind coal with a feed size of 0 to 50 mm. They can achieve a product fineness of 5% to 20% residue on a 90 µm sieve, depending on the coal’s characteristics and the desired combustion efficiency.
- Mining and Minerals Processing: The feed size for VRMs in mining applications depends on the specific mineral or ore being processed. Generally, the feed size can range from 0 to 100 mm, with the mills capable of producing a product fineness of 10% to 20% residue on a 45 µm sieve.
Strategies for Optimizing Feed Size
Pre-grinding: Implementing pre-grinding stages, such as using a hammer mill or a jaw crusher, can help reduce the feed size entering the VRM and improve grinding efficiency.
Material Blending: Mixing materials with different particle sizes can help achieve a more grinding efficiency.
What are the different types of roll mills
Vertical roller mills (VRMs) have gained prominence in various industries due to their versatility, energy efficiency, and ability to produce a consistent product quality. While the core functionality of grinding and separating materials remains consistent, different types of VRMs have been developed to cater to specific industry needs and applications.
Basic Vertical Roller Mill Design
Before delving into the different types of VRMs, it is essential to understand their basic design. A vertical roller mill consists of a grinding table mounted on a vertical axis, enclosed by a cylindrical drum. Grinding rollers are placed inside the drum, which are pressed against the grinding table by hydraulic or pneumatic systems. As the table rotates, the raw material is fed into the mill, where it is crushed into a fine powder by the grinding rollers. A dynamic classifier then separates the ground material, allowing only the desired particle size to pass through, while larger particles are returned to the grinding table for further processing.
Different Types of Vertical Roller Mills
-
LM Grinding Roller Mills
LM Grinding Roller Mills: These VRMs utilize high-pressure grinding rollers to exert additional force on the material, leading to increased grinding efficiency and a finer product. This type of mill is suitable for applications requiring fine grinding, such as cement, minerals processing, and chemical industries.
-
LUM Ultrafine Vertical Grinding Mill
LUM Ultrafine Vertical Grinding Mill: Developed specifically for slag grinding, these VRMs feature specialized grinding rollers and tables that can withstand the abrasive nature of slag. This design is ideal for industries like cement and steel, where slag is used as a supplementary cementitious material.
Key Features and Innovations
- Modular Design: Many modern VRMs feature a modular design that allows for the easy replacement of worn components, reducing maintenance downtime and costs.
- Wear-Resistant Materials: To increase the service life of grinding components, VRMs often employ wear-resistant materials, such as hardfaced grinding rollers and segmented grinding tables.
- Advanced Process Control: VRMs can be equipped with advanced process control systems that optimize grinding parameters, improve product quality, and reduce energy consumption.
- Environmental and Sustainability Efforts: Manufacturers continuously work to improve VRMs’ environmental performance by incorporating energy-efficient designs and reducing CO2 emissions.
Vertical Roller Mill Manufacturers
The increasing demand for energy-efficient and high-performance grinding solutions has led to the development and popularization of vertical roller mills (VRMs) across various industries. The success of VRMs is a testament to the relentless efforts of manufacturers in designing, engineering, and producing cutting-edge grinding equipment.
Leading Vertical Roller Mill Manufacturers
Zenith: based in China, is a leading VRM manufacturer.Zenith’s extensive experience in cement and mining industries has resulted in the development of the series of vertical roller mills, suitable for raw material, coal, and cement grinding.
Innovative Technologies and Design Improvements
Energy Efficiency: Modern VRMs are designed to consume less energy than traditional grinding systems, such as ball mills. Innovations like improved hydraulic systems, optimized grinding pressure, and advanced process control contribute to increased energy efficiency.
Modular Design: Many VRM manufacturers have adopted a modular design approach, allowing for easier maintenance and reduced downtime. This design enables the quick replacement of worn components and ensures the equipment’s long-term reliability.
Wear-Resistant Materials: To prolong the service life of VRMs, manufacturers have introduced wear-resistant materials for grinding components, such as hardfaced grinding rollers and segmented grinding tables, which can withstand abrasive materials and minimize wear.
Advanced Process Control: The integration of advanced process control systems in VRMs allows for real-time monitoring and optimization of grinding parameters, ensuring consistent product quality and reduced energy consumption.
Comprehensive Customer Support and After-Sales Service
Leading VRM manufacturers understand the importance of providing comprehensive customer support and after-sales services to ensure the optimal performance and longevity of the equipment. These services may include:
- Installation and Commissioning: Manufacturers often offer support during the installation and commissioning process, ensuring that the VRM is set up correctly and operates efficiently from the start.
- Maintenance and Repair: Regular maintenance is essential for the smooth operation of a VRM. Manufacturers provide maintenance services, spare
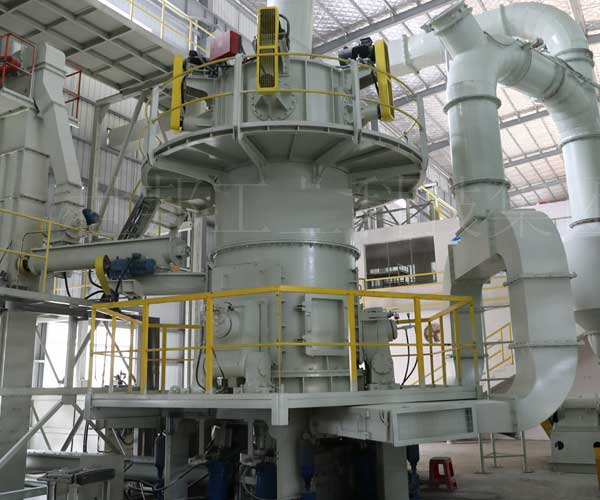
How To Select The Right Vertical Roller Mill Manufacturer
Vertical roller mills (VRMs) have become indispensable equipment in various industries, providing efficient and sustainable grinding solutions. With numerous VRM manufacturers worldwide, choosing the right one for your business can be a daunting task.
Assessing Your Needs and Requirements
Before beginning your search for a VRM manufacturer, it is essential to understand your specific needs and requirements. This assessment will help you identify the most suitable VRM type and manufacturer for your application. Consider the following factors:
- Industry and Application: Identify the specific industry and application for which the VRM will be used. Different industries, such as cement, power, and mining, have unique requirements that can affect the choice of VRM type and manufacturer.
- Feed Size and Product Fineness: Determine the feed size and desired product fineness for your application. These parameters will help you select a VRM that can efficiently process your raw materials and achieve the desired product quality.
- Capacity and Production Rates: Consider your production capacity and the required production rates to ensure the chosen VRM can meet your business’s demands.
- Budget Constraints: Assess your budget and investment capacity to help you identify a manufacturer that can offer a suitable VRM solution within your financial constraints.
Evaluating VRM Manufacturers
With a clear understanding of your needs and requirements, you can begin evaluating potential VRM manufacturers. Consider the following factors when assessing manufacturers:
- Experience and Reputation: Look for manufacturers with extensive experience in the VRM industry and a strong reputation for quality and reliability. Established manufacturers with a proven track record are more likely to deliver high-quality equipment and services.
- Technological Innovation: Seek out manufacturers that prioritize technological innovation and continuously improve their VRM designs to enhance performance, efficiency, and sustainability. Innovative manufacturers will provide you with cutting-edge solutions that keep your business competitive.
- Comprehensive Product Portfolio: Choose a manufacturer with a comprehensive product portfolio that offers a wide range of VRM types and sizes. This ensures that you can find a VRM solution that is tailored to your specific needs and requirements.
- Customization Capabilities: Select a manufacturer that can customize the VRM to meet your unique requirements. Customization options may include specialized grinding components, process control systems, or other features to optimize the VRM’s performance for your application.
Evaluating After-Sales Support and Services
A reliable VRM manufacturer should offer comprehensive after-sales support and services to ensure the optimal performance and longevity of your equipment. When evaluating manufacturers, consider the following after-sales services:
- Installation and Commissioning: Manufacturers should provide support during the installation and commissioning process, ensuring that the VRM operates efficiently from the start.
- Maintenance and Repair: Regular maintenance is crucial for the smooth operation of a VRM. Select a manufacturer that offers maintenance services, spare parts, and repair assistance to minimize downtime and maintain the equipment’s performance.
- Training and Technical Support: A reliable manufacturer should offer training and technical support to help your personnel operate and maintain the VRM correctly. This support may include on-site training, remote assistance, or access to online resources.
- Performance Monitoring and Optimization: Choose a manufacturer that provides performance monitoring and optimization services to ensure your VRM operates at peak efficiency. These services may include process audits, optimization recommendations, and the integration of advanced process control systems.