Limestone Grinding: An Overview of the Process
It is widely used in various industries, including construction, agriculture, environmental management, and metallurgy. Grinding limestone is a crucial process in many of these applications, as it helps to reduce the particle size of the raw material and make it suitable for the intended purpose.
The Importance of Limestone Grinding
Grinding limestone plays a significant role in its utilization across various industries. Some of the key reasons for grinding limestone include:
- Improved reactivity: Finer particles of limestone exhibit higher reactivity and faster dissolution rates, making them ideal for use in soil amendment, flue gas desulfurization, and other chemical processes.
- Enhanced workability: In the construction industry, finely ground limestone is used as a filler in cement and concrete mixtures. The reduced particle size improves the workability and strength of these materials.
- Easier transportation and handling: Grinding limestone reduces its volume and makes it easier to transport and handle, resulting in cost savings for manufacturers and suppliers.
Limestone Grinding Techniques and Equipment
Various grinding techniques and equipment are employed to reduce the particle size of limestone. Some of the most common methods include:
-
Ball mills: These cylindrical devices use steel balls as the grinding media, which are placed inside a rotating mill chamber. The limestone is crushed and ground as the balls impact the material, reducing its particle size.
-
Raymond mills: Also known as roller mills, these machines consist of a central vertical shaft that drives grinding rollers. The rollers crush the limestone against a grinding ring, creating fine particles.
-
Vertical roller mills: These mills use large rollers to crush the limestone against a rotating grinding table. The force of the rollers effectively grinds the material, yielding a finer particle size.
-
HGM series micro powder grinding mill: This mill is designed specifically for producing ultrafine limestone powder. It employs advanced grinding technology and a multi-layered grinding ring to achieve high output and low energy consumption.
Factors Influencing the Limestone Grinding Process
Several factors can impact the efficiency and effectiveness of the limestone grinding process. Some of these factors include:
- Material characteristics: The hardness and particle size distribution of the limestone feed can significantly affect the grinding process. Harder materials require more energy for grinding, while a narrow particle size distribution can lead to more efficient grinding.
- Grinding media: The type, size, and density of the grinding media used in the mill can influence the grinding efficiency. Optimal grinding media selection depends on the material characteristics and the desired final particle size.
- Mill operational factors: Mill speed, filling ratio, and residence time can impact the grinding process. Optimizing these factors helps to ensure efficient grinding and proper particle size reduction.
- Feed rate: The rate at which limestone is fed into the mill can also affect grinding efficiency. Feeding the material too quickly may overload the mill, while too slow a feed rate can result in inefficient grinding.
Limestone Grinding and the Environment
While grinding limestone is crucial for various industries, it is essential to consider the environmental impact of the process. Traditional grinding techniques can consume significant amounts of energy, contributing to a larger carbon footprint. Adopting energy-efficient grinding technologies, such as stirred media mills and high-efficiency classifiers, can help reduce energy consumption and contribute to more sustainable practices.
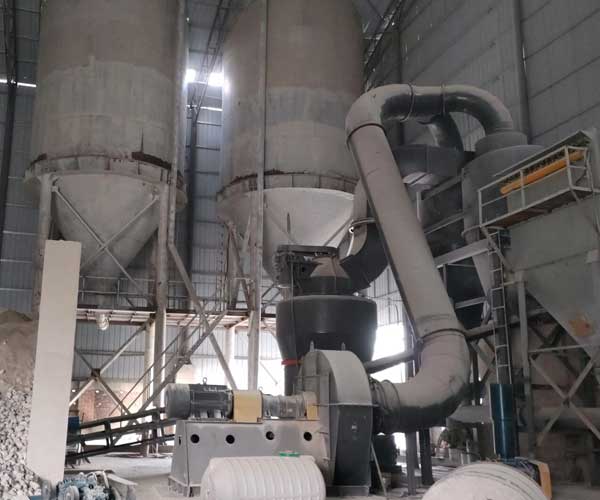
Addressing Energy Consumption Concerns in Traditional Grinding Mills
Environmental Impact of High Energy Consumption
High energy consumption in traditional mills has several negative environmental consequences, including:
- Increased greenhouse gas emissions: The energy required to operate grinding mills often comes from non-renewable sources such as fossil fuels, resulting in higher carbon dioxide (CO2) and other greenhouse gas emissions.
- Depletion of natural resources: High energy consumption contributes to the depletion of non-renewable energy sources and increases the demand for new energy infrastructure.
- Higher operational costs: High energy usage translates to increased operational costs for industries, reducing their competitiveness and potentially hindering growth.
- Waste generation: Inefficient grinding processes can lead to higher waste generation, as more material must be processed to achieve the desired particle size.
Potential Solutions for Reducing Energy Consumption
To address energy consumption concerns in traditional grinding mills, several strategies can be implemented:
- High-efficiency classifiers: These classifiers can improve the performance of traditional mills by separating fine particles from the grinding circuit, reducing the amount of material that must be reprocessed. This can result in significant energy savings.
- Stirred media mills: Stirred media mills, which use small grinding beads agitated by a rotating impeller, are more energy-efficient compared to traditional mills. They create a high-intensity grinding zone, breaking down particles through impact, attrition, and shear forces with reduced energy consumption.
- Optimization of mill operational parameters: Adjusting mill speed, filling ratio, and residence time can improve grinding efficiency and reduce energy usage.
- Improved grinding media selection: Choosing the appropriate type, size, and density of grinding media can enhance grinding efficiency, resulting in lower energy consumption.
- Advanced control systems: Implementing advanced control systems can optimize the grinding process by monitoring and adjusting operational parameters in real-time, resulting in reduced energy usage.
- Regular maintenance: Ensuring that grinding mills are well-maintained and operating efficiently can help minimize energy consumption.
Factors Affecting Energy Consumption in Limestone Grinding
Grinding limestone into fine particles is a crucial process for many applications, as it enhances its reactivity and application potential. However, energy consumption during the grinding process is a significant concern, as it affects both environmental sustainability and cost-effectiveness.
Material Characteristics and Their Impact on Energy Consumption
- Hardness: The hardness of limestone directly affects the energy required for grinding. Harder materials necessitate more energy to break down, resulting in increased power consumption.
- Particle size distribution: The initial particle size distribution of the limestone feed can significantly affect the grinding process. A narrow particle size distribution can lead to more efficient grinding, as fewer large particles need to be broken down, reducing energy consumption.
- Moisture content: The moisture content of the limestone feed can also impact the energy required for grinding. Higher moisture content may increase the energy needed to evaporate water during the process, leading to higher power consumption.
Grinding Equipment and Energy Consumption
Different types of grinding equipment exhibit varying levels of energy consumption. Some of the most common grinding mills used for limestone include:
- Ball mills: Ball mills use steel balls as the grinding media within a rotating chamber. These mills often consume a significant amount of energy, mainly due to the high friction between the grinding media and the material being processed.
- Raymond mills: Also known as roller mills, these machines consist of a central vertical shaft that drives grinding rollers, which crush the material against a grinding ring. Although more energy-efficient than ball mills, Raymond mills still consume considerable energy, particularly when processing harder materials.
- Vertical roller mills: These mills use large rollers to crush the limestone against a rotating grinding table. Although they offer some energy savings compared to ball mills and Raymond mills, their power consumption is still significant due to the compression and shear forces generated during grinding.
- Stirred media mills: Stirred media mills use small grinding beads agitated by a rotating impeller, creating a high-intensity grinding zone. These mills are generally more energy-efficient compared to traditional mills, as the limestone particles are broken down through impact, attrition, and shear forces with reduced energy consumption.
Operational Factors Affecting Energy Consumption
- Mill speed: The speed at which the grinding mill operates can impact the energy consumption. Higher mill speeds can lead to increased power usage, while lower speeds may result in inefficient grinding and incomplete particle size reduction.
- Filling ratio: The proportion of grinding media within the mill can also affect energy consumption. An optimal filling ratio ensures efficient grinding and reduces the energy required to achieve the desired particle size.
- Residence time: The amount of time the material spends in the grinding mill can impact the energy consumption. Longer residence times may result in over-grinding and increased power usage, while shorter residence times can lead to incomplete grinding and the need for further processing.
- Feed rate: The rate at which limestone is fed into the grinding mill can influence energy consumption. Feeding the material too quickly may overload the mill and increase power consumption, while too slow a feed rate can result in inefficient grinding and increased energy usage.
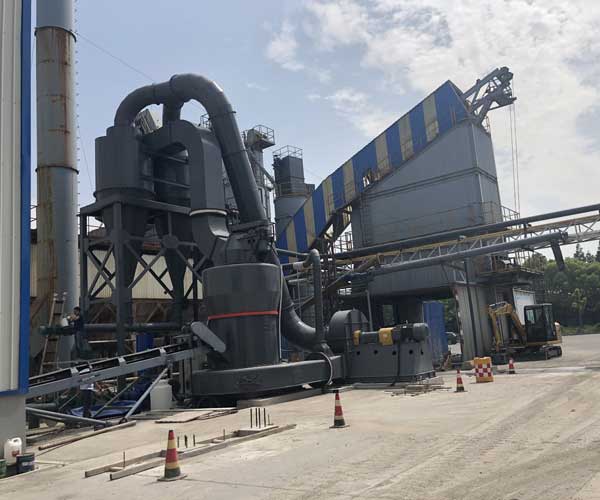
Low Energy Consumption Limestone Grinding Mills
Importance of Low Energy Consumption Limestone Grinding Mills
Low energy consumption limestone grinding mills are increasingly sought-after due to the following advantages:
- Reduced environmental impact: Low energy consumption grinding mills contribute to lower greenhouse gas emissions and decreased reliance on non-renewable energy sources, promoting environmental sustainability.
- Lower operational costs: Energy-efficient grinding mills help industries save on energy costs, which can be a significant part of their overall operational expenses.
- Enhanced competitiveness: Reducing energy consumption can improve the competitiveness of companies by reducing production costs and meeting the growing demand for environmentally sustainable products.
Principles of Low Energy Consumption Limestone Grinding Mills
Several grinding mill technologies focus on minimizing energy consumption while maintaining efficiency. These technologies include:
- Stirred media mills: Stirred media mills use small grinding beads agitated by a rotating impeller, creating a high-intensity grinding zone. The limestone particles are broken down through impact, attrition, and shear forces, resulting in reduced energy consumption compared to traditional mills.
- High-pressure grinding rolls (HPGR): HPGR technology employs two counter-rotating rolls to compress and grind the material. This method offers lower energy consumption and higher throughput compared to conventional grinding mills.
- Hybrid grinding systems: Hybrid grinding systems combine the benefits of two or more grinding technologies, such as HPGR and stirred media mills, to optimize energy efficiency and grinding performance.
Features of Low Energy Consumption Limestone Grinding Mills
Low energy consumption limestone grinding mills offer several features that contribute to their energy efficiency, including:
- Advanced grinding mechanisms: These mills utilize grinding mechanisms that reduce friction and energy loss, such as the use of small grinding beads in stirred media mills or the compressive forces in HPGR technology.
- Optimized operational parameters: Low energy consumption mills are designed to operate at optimal speeds, filling ratios, and residence times, ensuring efficient grinding with minimal energy usage.
- Intelligent control systems: Advanced control systems monitor and adjust operational parameters in real-time, optimizing the grinding process and reducing energy consumption.
- High-efficiency classifiers: Incorporating high-efficiency classifiers in grinding mills can improve performance by separating fine particles from the grinding circuit, reducing the amount of material that needs to be reprocessed and resulting in energy savings.
Case Studies: Successful Implementations of Low Energy Consumption Grinding Mills
-
20TPH Limestone Grinding Plant
Raw Material:Limestone
Capacity:20TPH
Input Size: 0-5mm
Output Size: 200 MeshD90,180 MeshD98
Application: Used to produce waterproof coating
Equipment:MTW175Grinding Mill, MTW138 Grinding Mill
-
2,000TPD Limestone Grinding Plant
Material: Limestone
Input Size: <50mm
Output Size: 200 mesh
Capacity: 2,000 tons a day
Application:Aerated brick
Equipment: MTW175Z European Trapezium Grinding Mil, pulse dust remover, feeder, PLC system
-
India 30TPH Limestone Grinding Plant
Material: Limestone(0-12mm) (CaO > 81.6%,humidity < 0.1%H2O)
Output Size: 74μm (200mesh) D90
Equipment: 3 sets of MTW138 European Mill
Application: The finished product will be used for power plant desulfurization
-
Mongolia 300,000TPY Limestone Grinding Plant
Material: Limestone
Capacity: 300,000TPY
Daily Operation: 24h
Input Size: below 35mm
Output Size: 250-325mesh
Application: Desulfurization agent in coal-fired power plant
Equipment: 3 sets of MTW215 mill